سانتریفیوژ دکانتر تجهیز پیشرفته ای است که در جداسازی جامد از مایع در یک فرایند پیوسته عمل می کند. فرایند جداسازی با استفاده از نیروی گریز از مرکز در محفظه بول اتفاق می افتد و محلول شفاف شده با چرخش اسکرول به خروجی تجهیز هدایت می شود.
دکانتر سانتریفیوژ فرایند جداسازی دو فاز جامد از مایع یا مایع از مایع را در صنایع مختلف را انجام می دهد که شرکت دانش بنیان همگام صنعت بیش از یک دهه جهت براورده کردن این نیاز صنایع با علم و تلاش مهندسین خود دست به کار شده و این تجهیز پیشرفته را به بازار ارائه داده است .
سانتریفیوژ دکانترهای تولید همگام صنعت جهت جلوگیری از خوردگی به هنگام تماس با سیال، از فولاد با عیار بالا ساخته شده اند .
دکانتر سانتریفیوژ تجهیزی پیشرفته است که با پردازش مداوم و کارآمد فرایند جداسازی مایع از جامد را انجام می دهد.
نیروی گریز از مرکز تولید شده از چرخش بول با بدنه فولادی و سرعت چرخش اسکرو فرایند جداسازی مایع از جامد شکل می گیرد.
از آنجایی که بسیاری از قطعات از نظر ساختار پیچیده هستند و با فناوری پیشرفته و دقیق ساخته می شوند، جهت کنترل و رفع ارتعاشات، تحمل ابعادی و هندسی تجهیز پس از کارکرد ، تعمیر و نگهداری و سرویس سانتریفیوژ دکانترها توسط مهندسان مجرب شرکت همگام صنعت انجام می پذیرد.
دکانتر سانتریفیوژ تجهیزی است که عملیات جداسازی و ته نشینی را انجام می دهد . در فرایند جداسازی، دکانتر سانتریفیوژ با چرخش و دوران با سرعت بالا موجب ته نشینی ذرات جامد معلق در فاز مایع شده و ذرات چگال تر با نیروی گریز از مرکز به خارج از تجهیز هدایت می شوند.
جداسازی جامد و مایع در یک دکانتر سانتریفیوژ بر اساس اصل نیروهای گرانشی کار می کند. در حالی که جداسازی گرانشی یک مخلوط گلی (به پایین) و آب (به سمت بالا) در فن آوری های جداسازی مبتنی بر جداسازی 1xG مانند ظرف استاتیک، زلال ساز یا جداکننده لامال، زمان قابل توجهی نیاز دارد. چرخش یک سانتریفیوژ این اصل گرانشی را تا حد زیادی سرعت می بخشد.
در واقع، نیروی G تولید شده توسط یک سانتریفیوژ دکانتر میتواند بیش از سه هزار برابر بیشتر از گرانش باشد و فرآیند جداسازی را از ساعتها به ثانیهها کاهش دهد. سانتریفیوژهای امروزی یک فناوری از نوع ضد جریان هستند. فرآیند جداسازی در یک سانتریفیوژ دکانتر 2 فاز باعث می شود که ذرات جامد متراکم تر، متراکم شده و در درام داخلی ته نشین شوند و سپس از طریق انتهای تخلیه جامدات از دکانتر منتقل و خارج شوند. در یک سانتریفیوژ 3 فاز، سیستم بافل در داخل سانتریفیوژ ساخته می شود. سیستم بافل مانع از تخلیه روغن با آب می شود. روغن (مایع فاز سبک تر) بین دو بافل جمع آوری شده و از روی آن جدا می شود.
جداسازی جامد از مایع یک فرآیند تولید متداول است و همگام صنعت بیش از 15 سال تجربه در تولید دکانتر سانتریفیوژ برای برآورده کردن این نیاز در صنایع مختلف تلاش می کند.
سانتریفیوژ دکانتر چیست؟
سانتریفیوژ دکانتر تجهیزی است که منجر به جدایش ذرات سالید معلق در یک سپانسیون یا اسلاری از فاز مایع می شود، علاوه برآن، دکانتر سانتریفیوژ می تواند باعث جدایش دو فاز مایع مثل روغن و آب هم بشود، اصول کار آن براساس سرعت ته نشینی ذرات می باشد که ذرات بزرگتر و چگال تر سرعت بیشتری در ته نشینی دارند .
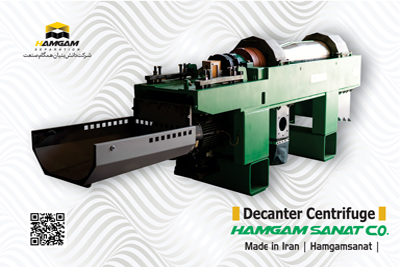
دکانتر سانتریفیوژ چگونه کار می کند؟
سرعت سانتریفیوز دکانتر براساس نیروی حاصل از دوران بول بوده و لذا سرعت ته نشینی یا جدایش بسیارافزایش پیدا می کند و باعث می شود که بتوان جداسازی فاز جامد از مایع را در یک اسلاری یا سپانسیون در حجم بالا و بطور پیوسته جدا کرد، مزیت حجم بالا و پیوستگی دو مزیت دکانتر نسبت به دیگر سیستم های جداکننده می باشد .
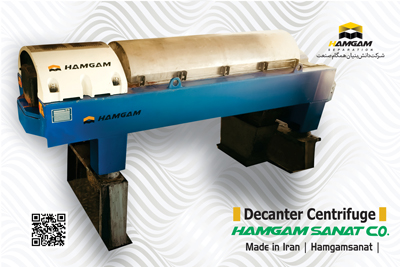
قطعات سانتریفیوژ دکانتر:
Bowl : با دوران بول، جدایش فاز جامد از مایع صورت می پذیرد.
Beach : باعث آب زادیی از کیک یا جامد می شود و منجر به خروج مایع از سرریزهای( weirs ) هاب مایع می شود.
Screw conveyor : وظیفه انتقال کیک به خروجی را دارد .
Gear box : وظیفه آن ایجاد اختلاف سرعت بین bowl و screw می باشد.
سرعت دوران:
2000rpm
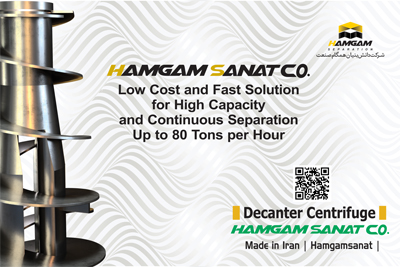
سیال وارد شده در دکانترسانتریفیوژ چیست؟
دکانتر سانتریفیوژ می تواند هرگونه اسلاری (سیال حاوی ذرات سالید) که قطر ذرات بالاتر از 10 میکرون باشد را جدا کند محدوده 10 تا 10000 میکرون محدوده مناسبی برای جداسازی از طریق دکانتر می باشد ، در این مورد خاص دکانتر طراحی شده برای شرکت اروند از 33 تا 500 میکرون کاربرد دارد
اسلاری : PVC+ water suspension
ابعاد:
4432*3140*2130= L*W*H (دکانتر آندریتز اروند( ساخت شرکت دانش بنیان همگام صنعت))
ویژگی منحصر به فرد:
- جداسازی در حجم بالا
2- پیوستگی در جدا سازی یعنی اسلاری (PVC- slurry) بطور پیوسته وارد دکانتر می شود و جداسازی صورت می پذیرد
قایلیت های تنظیم :
Weir ها یا پورت های خروجی مایع قابل تنظیم می باشد، این تنظیم باعث تنظیم شرایط عمیاتی محصول از قبیل میزان خشک بودن کیک خروجی می گردد
راندمان سانتریفیوژ دکانتر:
تابع شرایط عملیاتی و خواسته مشتری می باشد، در واقع راندمان یک خواسته عملیاتی مشتری می باشد که دکانتر متناسب با آن طراحی می گردد .
نویز و ارتعاش:
وضعیت کیفی ارتعاش
|
محدوه ارتعاشی (میلیمتر بر ثانیه)
|
خوب
|
0-14
|
مفید
|
14-18
|
قابل قبول
|
18-22
|
غیر قابل قبول
|
22-26
|
شاخص مقاومت در مقابل سیال و هوا:
بکارگیری متریال های مقاوم به خوردگی در قطعات اصلی مثل بول، اسکرو و هاب ها
,1.4470 برای بول و هاب ها و 1.4571 برای اسکرو
- فناوری محصول:
- روتور : که چرخش دو سازه بول و اسکرو می باشد که اسکروه حدود 50 دور بر ثانیه کمتر از بول می چرخد
- گیربکس که وظیفه تامین گشتاور و اختلاف سرعت مورد نیاز فرایند را تامین می کند، گیربگس از نوع خورشیدی با نسبت تبدیل (i=40) می باشد
انتخاب متریال:
,1.4470 برای بول و هاب ها و 1.4571 برای اسکرو
فرایند طراحی محصول:
- طراحی سیستمی: در این مرحله از طراحی الزامات عملیاتی مشتری، شناسایی، تصدیق و نهایی می شود و همچنین پیکره بندی فناوری های پاسخ دهنده استخراج و انتخاب می شوند
- طراحی تفصیلی : براساس الزامات عملیاتی فاز قبل طراحی تفضیلی قطعات و زیر مجموعه ها انجام می پذیرد که خروجی این فاز اسناد بسته دانش فنی محصول می باشد(Technical data package= TDP ) می باشد
- ساخت: در این مرحله ساخت قطعات و مجموعه مطابق با بسته دانش فنی صورت می گیرد و تستهای کارخانه روی آن انجام می پذیرد
- بهره برداری : در این فاز تجهیز بسته بندی، ارسال، نصب و مورد بهره برداری قرار می گیرد
- پشتیبانی : در این فاز تجهیز مورد بازدید های دوره ای واقع می شود و پشتیبانی های مورد نیاز صورت می پذیرد
- وارهایی : در این فاز که انتهای چرخه عمر می باشد تجهیز چنانچه لازم باشد که از رده خارج شود با رعایت الزامات زیست محیطی این کار صورت می پذیرد.